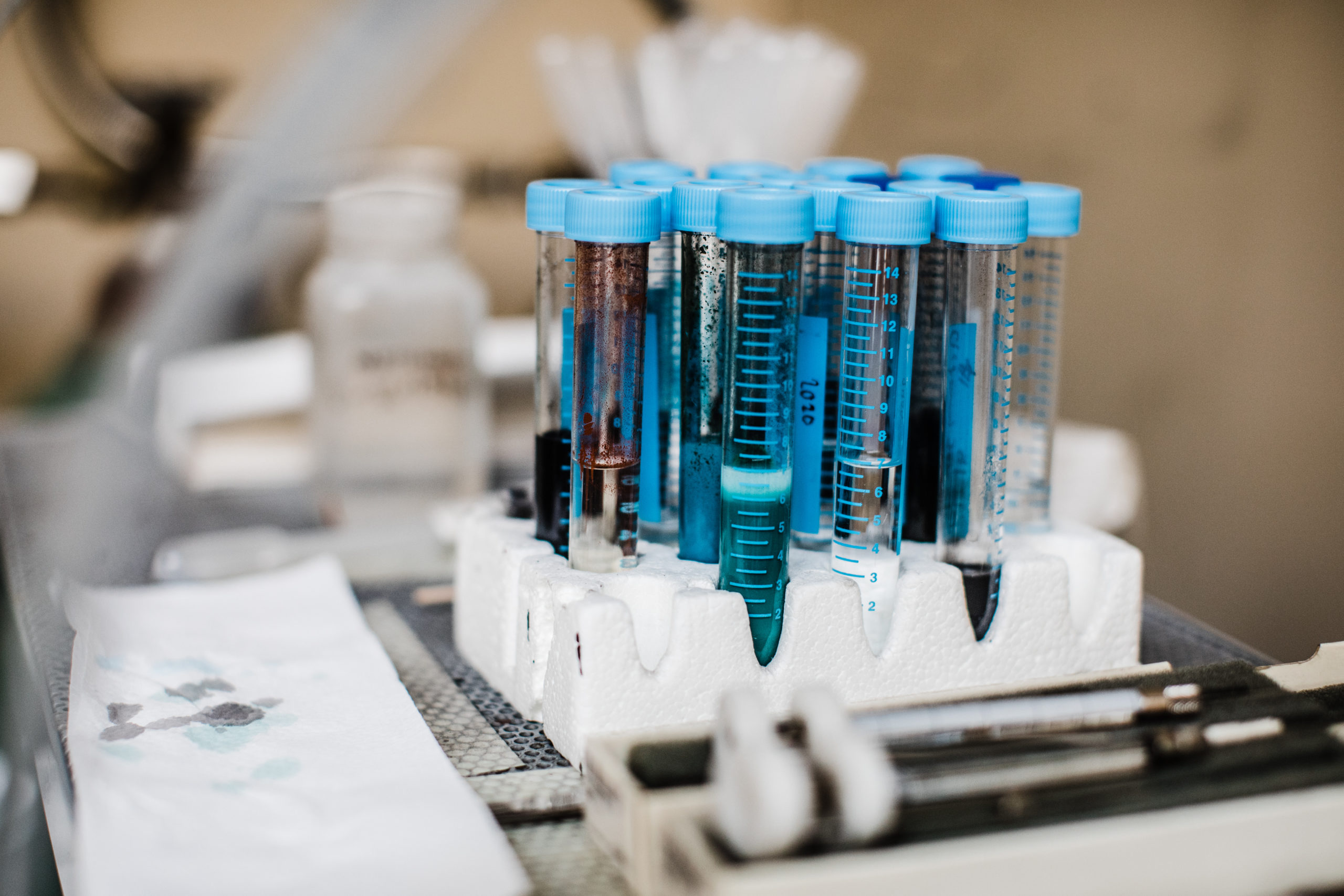
A large Midwestern manufacturer of steel furniture, who sources subcomponents from multiple suppliers, was frustrated with the loss of product and costs associated with rework. Due to coating adhesion, surface wetting and coverage issues on subcomponents they were realizing unacceptable rework rates and labor costs.
The outsourced components consisted of medium to heavy gauge stampings with additional punch, drilling and threading steps. Depending on the component supplier, as much as 40% of final products required costly material, labor and production time to address rework due to surface metal working fluid residue affecting application performance on the final assembled parts.
The question to Marcus Paint? “Can you simply put something in our paint to make it cover and adhere to all our components regardless of where we source them? One answer could be yes, but that wouldn’t be in our client’s best interest causing increased material costs. That’s a “Treat the symptom not Cure the illness” solution.
A wash system and dry off oven would have addressed the issue; however, our client had no real estate available to put one in place. Further, a wash system had not been necessary for their application as their suppliers all have Part Washing Systems to handle high volume-bulk processing. These had, in the past, typically presented suitable levels of cleanliness for our client’s use.
Discovery:
Marcus’ Sales and Technical Account Managers sat down with this client to understand what they were sourcing, from whom, their processes, materials and rework data by supplier.
The team then worked with each subcomponent supplier to determine what the problem statement was to be so we could get to work on a solution or corrective action.
The subcomponent suppliers all used various Metal Working Fluids which are as necessary to the process of working steel as the steel itself. There are a variety of these fluids consisting of; Synthetic, Semi-Synthetic and Water-Soluble Oils (Emulsified). They must be utilized to control heat and friction, increase tooling life, displace debris, provide short term corrosion prevention and maintain specific part integrity.
Approach & Corrective Action:
Marcus Paint used a quality tool, Root Cause Analysis, to brainstorm the problem which was stated as:
Inconsistencies in subcomponents being fabricated for our client were resulting in poor paint performance.
After collaboration with our client’s subcomponent vendors the following were determined to be contributors and solutions:
- Each subcomponent manufacturer was using a different metal working fluid at various reduction ratios/concentrations. It’s important to note that these vendors had to utilize what worked to fabricate the parts they were producing. It’s not as simple as suggesting a change to x or y. Lab work had to be performed to determine where the tolerance thresholds were to obtain fabrication results yet obtain necessary cleanliness results as well.
- Each subcomponent manufacturer utilized different cleaning equipment contributing to varying results. (i.e. High Pressure Spray, Immersion-Rotary, Media Wash)
This was more challenging then the fluid problem. We focused on developing specifications relative to the outcome of their cleaning processes. Standard Operating Procedures to calibrate all the suppliers for cleanliness outcome standards through understanding and controlling specific, mechanical energy & power density capabilities, optimal operational temperature ranges, common family powder detergents and process time. Managing maintenance and bath change out scheduling also played a role in the solution.
Essentially, we educated the subpart vendors on how their activities impacted the coatings performance down the line and assisted them in determining the adjustments necessary for them to obtain the target cleanliness specification. This also ensured they could identify and solve these issues on their own in the future.
Correction: Collaboration with the subpart vendors to establish an “Outcome/Cleanliness Specification” and the Procedures to obtain those results.
Outcome:
These efforts resulted in a 40% reject-rework rate to less than 5%. This reduction in costs had a significant contribution to our client’s bottom line.
Is this Rocket Science? No, but it does entail a significant investment in time and attention to detail in understanding upstream and downstream issues or inconsistencies that may affect our client’s coating operations.
Tools Utilized:
- Root Cause Analysis
- Standard Operating Procedures
- Work instructions & training initiatives
- Subcontractor internal auditing measures and reporting
- Client auditing reporting performance and compliance to standards through statistical online data.
- In some circumstances, Marcus Modified – Client Specific PFMEA: Process Failure Mode Effects Analysis.
This is the Marcus difference….expertise, discovery, planning, execution and validation measures. We are not simply our client’s paint vendor; we are their strategic partner.