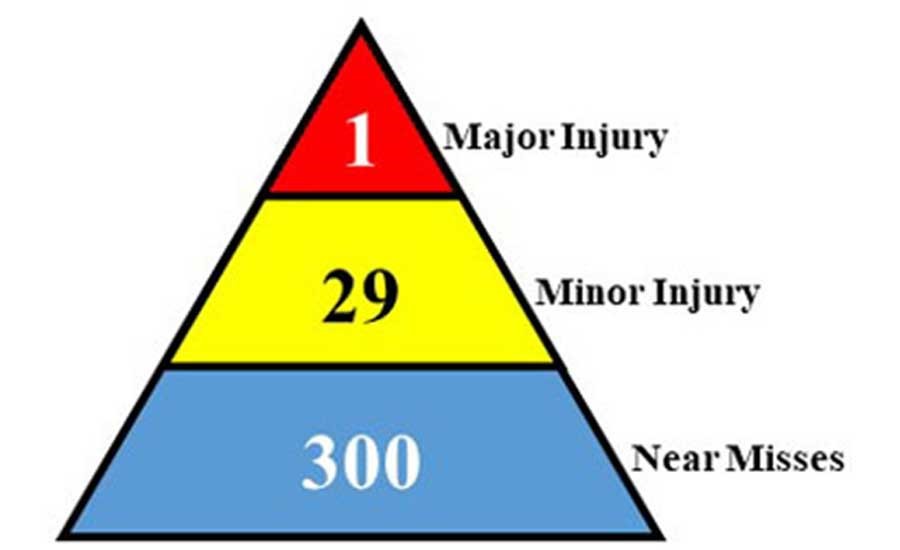
We’re Glad You Asked!
Employees may prefer to avoid reporting when an incident, near-miss, or accident occurs, especially if they contributed to the issue and may face consequences. However, educating the workforce about the “why” can reduce the stigmas of reporting these events.
These three terms are sometimes used interchangeably but each has a different meaning1. Let’s look at how to use the correct terms to describe the event and create accurate reporting:
- Incident: Refers to an unexpected event that did not cause injury or damage but had the potential to do so.
Example: A pressure valve malfunctions and releases liquid. The valve was replaced without injury to anyone, and no damage occurred.
- Near-miss: An unanticipated occurrence that might have resulted in physical harm or property damage but didn’t.
Example: A box is on the floor in the way of foot traffic. Someone walking through with their arms full might not have seen the box until it was too late and could’ve tripped. Another employee saw it first and moved the box, removing the potential for a trip hazard.
- Accident: An unfavorable incident that occurs unintentionally, without warning, and usually causes damage or injury.
Example: A forklift driver doesn’t have the lift in the proper position while carrying a drum full of oil. The drum falls off, resulting in a total loss of the oil and drum, plus the labor and spill kit costs spent for the cleanup.
Reducing unsafe occurrences has long been a focus for employers; after all, it has a catastrophic effect on the company’s bottom line. OSHA estimates employers pay almost $1 billion each week for direct costs alone, including worker’s compensation payments, medical and legal expenses. This estimate does not include the indirect costs such as time spent on training, replacing employees, lost productivity, absenteeism, property or equipment repair, and time spent on investigations and implementing corrective measures.2
Herbert Heinrich, a health & safety leader in the insurance industry, proposed a theory in 1931 that states for every 300 unsafe behaviors performed, there are 29 minor accidents and one serious accident.3
He demonstrates his theory in a triangle form, referred to as the Heinrich or Safety Triangle. The further up the triangle, each level represents an increase in the type of unsafe occurrences.
In 1966, Frank Bird contributed further to Heinrich’s theory. After analyzing 1.7 million accident reports from almost 300 companies, His data showed the 300:29:1 rule and the corresponding triangle could be expanded with additional levels. His updates to the triangle demonstrate the link between the number of near misses to the number of significant casualties.4
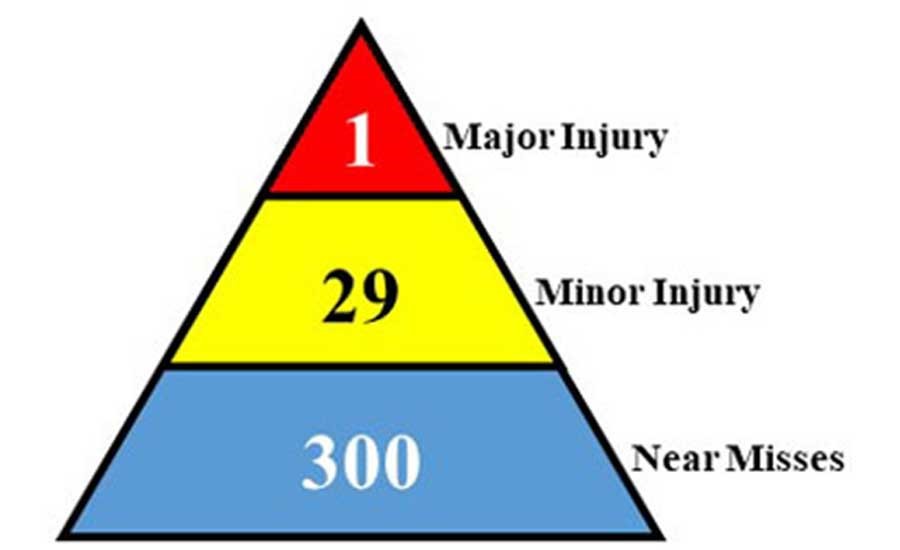
Figure 1: Heinrich’s Original Triangle
The triangle provides a great visual to see how one simple unsafe decision can escalate into something with more dire consequences, even leading to life-altering results and the most severe as a workplace fatality. Understanding types of events and the links between them leads us to the next step to understanding why reporting is crucial:
So why should employees report occurrences, even the small ones? Once again, I’m glad you asked!
- It can identify potential hazards in the workplace and provide the opportunity to take appropriate action to remove the hazard before it results in a more serious outcome.
- Organizations can address the root cause of the issue, rather than just fixing the symptoms.
- Tracking incidents, near-misses, or accidents demonstrates the company’s commitment to safety.
- The risk factor decreases for the same issue to be repeated.
- Provides an outlet for all employees to actively participate and contribute to workplace safety.
- It identifies opportunities for improvement including training, updates to outdated procedures, using new methodologies, or the need for equipment upgrades.
- The company complies with regulatory requirements applicable to their industry or workplace.
When employers educate their workforce on the “why’s”, employees may feel more empowered to report events. It also encourages accountability and involvement for the good of the entire organization, and employees may feel a sense of pride and ownership for making a difference in their company.
We’ve discussed some of the “Why’s”, but the “How” that causes unsafe acts and other severe occurrences should also be considered. A few examples include:
- Employees rushing through a process or being distracted.
- Not following established protocols or procedures or taking shortcuts.
- Knowingly operating equipment without safety guards in place or when equipment is broken or defective.
- Using equipment in a manner it was not designed or intended for.
Marcus Paint has an established process to report occurrences and utilizes software to log all occurrences. This allows us to:
- track the review process.
- identify valuable data points about the processes, equipment, training needs, etc.
- develop metrics for the entire process.
Finding solutions and improving the workplace can’t be achieved by just changing processes; it requires everyone’s commitment and involvement to get there. Our employees participate in various activities to support safety initiatives:
- Quality and Safety Councils: are made up of employees across multiple departments. Through the councils, they perform root cause analysis, inspections, investigations, etc. to determine appropriate corrective measures.
- Suggestion box: Employees can report issues, concerns, or improvement ideas in a conveniently located box for further review by the Councils or management.
- Open door policy: The accessibility to owners and management creates a relaxed culture where employees can feel more comfortable approaching management with their concerns or known safety issues.
- 6S inspections: Employees participate in a rotating schedule to inspect various work areas to provide feedback, using the Kaizen methodology. This has been a valuable source of information to identify issues where the potential for a safety infraction or equipment failure could have occurred.
The work culture at Marcus Paint uses the combination of establishing expectations, providing education, and obtaining employee involvement to minimize further unwanted occurrences and encourage continued improvements for a safer and healthier workplace.
1 Macpherson, S. (2023, June 20). Why track incidents, near-misses, and accidents?
https://www.thechecker.net/stories/blog/why-track-incidents-near-misses-and-accidents
2 (N.d.). https://www.osha.gov/businesscase/costs
4 Editor. (2024, January 19). Safety triangle “The safe pyramid.” OSHA Outreach Courses. https://www.oshaoutreachcourses.com/blog/safety-triangle-the-safe-pyramid/